- Home
- >
- Products
- >
- Powder Pneumatic Conveying System
- >
- Double Silo Dense Phase Bin Pump
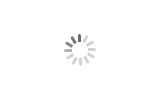
Double Silo Dense Phase Bin Pump
Brand :Cafu
Product origin :China
As a continuous powder conveying silo pump, has the characteristics of reliable technical level and advanced technology. The equipment is widely used in electric power, cement, food, metallurgy and other industries.
The continuous delivery bin type pump sold by the company is composed of two pump bodies, which are controlled by the pipeline cutting valve to maintain the continuity of pipeline delivery. In many cases of powder pneumatic conveying system engineering, we maintain strong technical advancement and more practical experience.
Principle introduction: in fact, it uses the principle of pneumatic pressure difference to transport. After the material enters the pump body, when it is filled with powder, the material forms a fluidization state after gasification. Through the mixing chamber, the compressed air is spewed out at high speed through the jet nozzle, and the fluidization powder is fully mixed evenly. Two warehouse type pumps can feed at the same time, feed in turn, transport materials alternately, pipeline can achieve uninterrupted transmission of powder, to meet the requirements of large throughput, is a reliable process for improving the capacity of powder pneumatic conveying system.
Double silo dense phase bin pump
Product Introduction:
The pneumatic conveying system with two silo pumps working continuously is an advanced pneumatic conveying equipment.
The system has novel structure, stable performance, reliable operation, high degree of automation (PLC control), simple operation, low maintenance cost and low comprehensive operation cost. The whole pneumatic conveying system has the characteristics of low energy consumption, low wear, high ash - gas ratio and high conveying rate.
Double bin pump operation mode: continuous, discontinuous. Wide adaptability of air source pressure, working pressure is 0.15-0.45mpa, depending on the conveying distance and throughput. Conveying distance < 1000m, height < 42m, conveying capacity ≤200t/h, temperature -20℃-150℃, conveying air volume, pressure and conveying pipe size, also change with the conveying capacity and conveying distance.
Product features:
1, ash gas ratio can reach more than 40kg/kg, so the gas consumption is low.
2, powder in the conveying process of the pipeline impact wear is small.
3, the powder in pneumatic conveying gas consumption is low, less exhaust gas emissions, can reduce the investment in tail gas treatment equipment.
4, the size and humidity of the powder is not high.
The device can be widely used in:
1. Dry dedusting process system of electrostatic precipitator and bag filter in thermal power plant, conveying process system of industrial raw materials such as building materials and clinker;
2. Powder material conveying process system in metallurgical industry;
3. Transportation process system of powdery materials and light particles in petroleum, chemical, food and other industries;
4. Rice husk transportation process system in food processing industry;
5. Dry ash conveying process system of biological kitchen waste power plant;
6. Ash silo construction and auxiliary equipment of ash silo;
7. As a pneumatic conveying equipment of petroleum coke powder combustion process system.
Model Specification | |||||||
Specification | LB-1.0 | LB-1.5 | LB-2.5 | LB-4.0 | LB-6.0 | LB-8.0 | |
Effective volume of pump body | m3 | 1 | 1.5 | 2.5 | 4 | 6 | 8 |
delivery capacity | m3/h | 10~15 | 15~20 | 20~30 | 35~45 | 45~85 | 65~120 |
displacement of air compressor | m3/min | 10 | 12~15 | 15~20 | 20~40 | 20~40 | 40~60 |
working pressure | Mpa | 0.2~0.45(It varies with the transmission distance) | |||||
conveying distance | m | 100~1500(Refers to the equivalent distance after conversion) | |||||
working temperature | ℃ | -19~200,Working temperature over 120℃ for special products,please | |||||
main material of pump body | 16MnR |
Customized design of general fabricated steel silo needs to provide: 1. Storage material name 2. Density of storage material 3. Storage material particle size 4. Storage capacity 5. Feeding method 6. Discharge method and size of discharge port 7. The height of the discharge port from the ground...more